21/01/2022
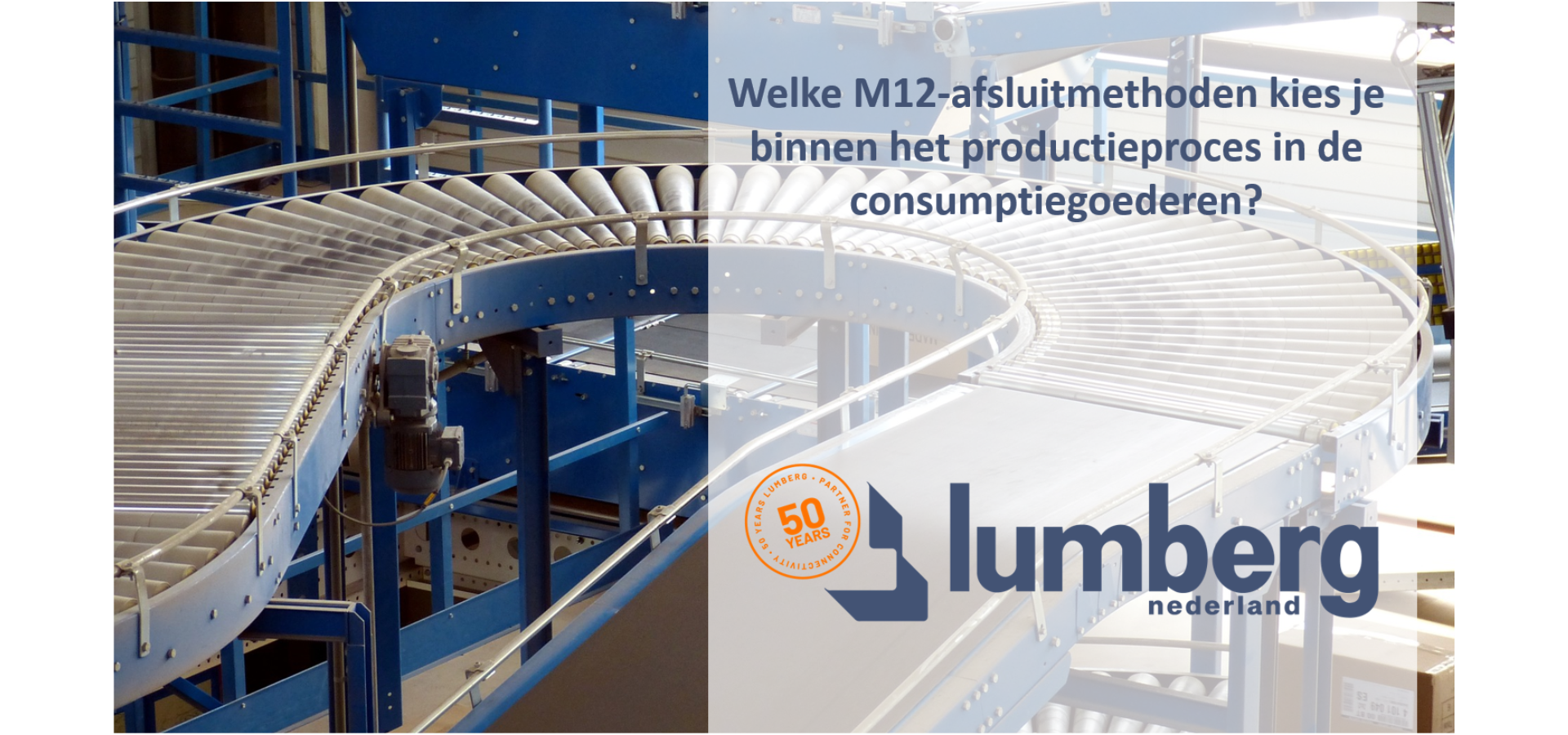
Which M12 Termination Method Should You Choose?
In many automation applications, the importance of “the connector” is often underestimated, including in industrial automation. From the production processes in consumer packaged goods (CPG) to the cloud, connectors impact performance at every level of an automation network.
IIoT environments demand smart devices—PLCs, IPCs, human-machine interfaces (HMIs), robots, cameras, sensors, and more. All of these devices need to connect to the network. If it’s a wired connection, then the device will also need a connector. This connector acts as an essential link between network nodes.
Reliability
Although M12 connectors were originally designed for sensor signal processing, they have become vital in industrial power and data transmission applications. They are used to connect components like sensors, actuators, switches, PLCs, and I/O-boxes.
This connectivity technology is crucial for capturing, processing, and transmitting data from increasingly intelligent machines. These systems support automated, responsive decision-making in production processes. Data must be transmitted through highly reliable, high-speed connections that can withstand elements like dust, noise, extreme temperatures, and vibrations. The M12 connector provides the speed, reliability, and robustness needed in today’s automation environments and offers connectivity that supports:
- Lower maintenance costs
- Increased safety
- Enhanced efficiency
- Reduced downtime (In CPG environments, reducing downtime is essential, as even a few minutes of lost production can lead to significant raw material waste.)
M12 Termination Methods and Their Importance
Field-attachable connectors are ideal for applications where cable lengths can’t be predetermined. This type of connector allows for on-site cable cutting to the required length before attaching the connector.
There are three classic M12 termination methods for connecting cables to M12 connectors in the field. Whichever option you choose, the first step is always to prepare the cable for connection. Begin by sliding the gland, handle, and housing over the cable to secure it after stripping.
The termination method can affect connector performance and the amount of repair work required by maintenance teams. Here’s an overview of these three classic termination methods:
1. Insulation Displacement Contact (IDC) Termination
IDC termination, also known as self-locking, allows for a quick, easy installation and is the most popular termination method in industrial and harsh environments.
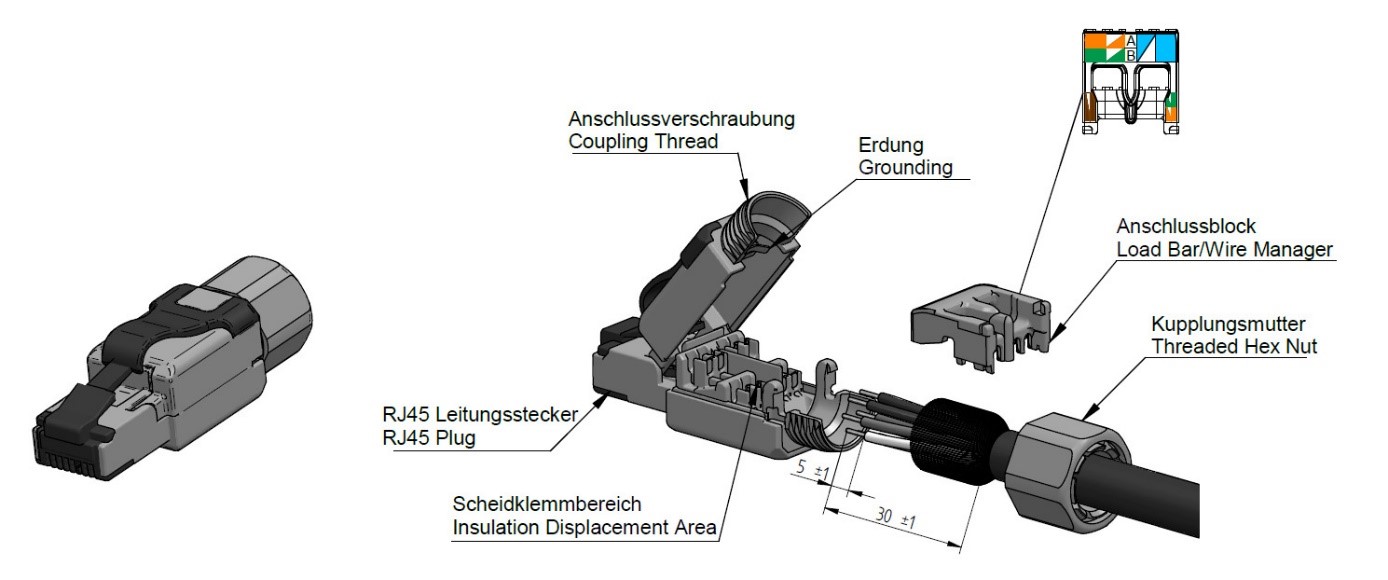
2. Screw Termination
The screw termination method is a classic technique that has been used for several years.
The process begins with preparing the cable for assembly. After stripping the cable jacket, individual wires must be stripped to ensure reliable contact. Stripped wires require additional ferrules, which must be crimped before inserting them into the contact holes of the cable socket or plug.
Attention to detail is crucial in the final assembly step, as this is one of the most important stages to maintain the integrity of the sealing system.
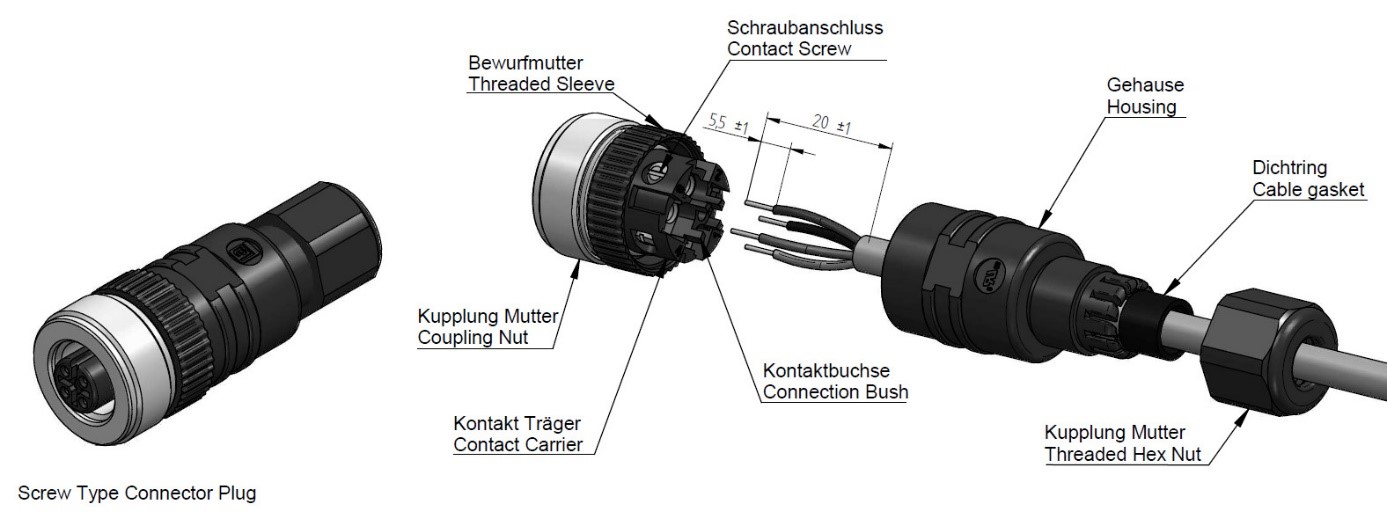
Choosing the Right M12 Termination Method for the CPG Market
In most industrial automation environments, including the CPG sector, selecting the right termination method means balancing cost, reliability, and installation time. Here are some guiding questions:
- What are the maintenance requirements?
- How often will connectors need to be replaced?
- Do I need to meet a specific IP rating?
- What are the vibration levels in my environment?
- How much time do we have for installation at each node?
- What is our budget for connectors?
Different nodes within the same application may have entirely different requirements. For this reason, the CPG market demands unique connectivity solutions and M12 termination methods tailored to location-specific needs. Lumberg Nederland supports these needs through our customization program.